Summary
Electrostatic coating application offers benefits for shipyards seeking to enhance both environmental performance and operational efficiency. By increasing transfer efficiency and minimizing overspray, the technique significantly reduces airborne paint particulates to create a cleaner workspace and improve safety for application crews.
Source: Marine Log
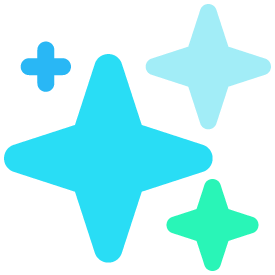
AI News Q&A (Free Content)
Q1: What is electrostatic coating application, and how does it benefit shipyards in terms of environmental performance and operational efficiency?
A1: Electrostatic coating application is a process where paint or other coating materials are charged with an electrical current and sprayed onto a substrate, which is grounded. This method offers several benefits to shipyards, including increased transfer efficiency and reduced overspray. By minimizing airborne paint particulates, it creates a cleaner workspace, enhances safety for application crews, and contributes to better environmental performance by reducing pollution.
Q2: How does Industry 4.0 impact the operations of modern shipyards, and what role does electrostatic spraying play in this transformation?
A2: Industry 4.0 represents the integration of digital technologies into industrial processes, leading to more automated and efficient shipyards, known as Shipyards 4.0. Electrostatic spraying fits within this transformation by providing a more precise and efficient method of applying coatings, which aligns with the goals of improved productivity and reduced environmental impact. The implementation of smart technologies, including augmented reality and cyber-physical systems, further enhances operational capabilities.
Q3: What are the technological advancements in electrostatic spray systems utilized in shipyards?
A3: Recent advancements in electrostatic spray systems include the development of more efficient spray guns and nozzles that enhance coating application precision. These systems are equipped with advanced sensors and control mechanisms to optimize the spray pattern and reduce wastage. Additionally, they are integrated with digital monitoring systems to ensure consistent application quality and to provide real-time data for process optimization.
Q5: What are some of the challenges faced by shipyards in adopting electrostatic spray technology, and how can they be overcome?
A5: Challenges in adopting electrostatic spray technology include the initial cost of system implementation, the need for skilled personnel to operate and maintain the equipment, and the integration of new systems into existing workflows. These challenges can be overcome through targeted training programs, phased implementation strategies that allow gradual adaptation, and collaborations with technology manufacturers for ongoing support and updates.
Q6: What role do regulatory organizations play in the adoption of environmentally friendly technologies like electrostatic spraying in shipyards?
A6: Regulatory organizations play a crucial role in promoting the adoption of environmentally friendly technologies by setting standards and guidelines that encourage or mandate the use of such technologies. They provide frameworks that ensure compliance with environmental regulations, offer incentives for the adoption of sustainable practices, and facilitate research and development in cleaner technologies.
Q7: What are the potential cost savings for shipyards that implement electrostatic spray technology, and how does it compare to traditional methods?
A7: Shipyards that implement electrostatic spray technology can experience significant cost savings due to reduced paint wastage and lower environmental compliance costs. This method increases transfer efficiency, meaning less paint is required for the same coverage, and reduces the need for extensive cleanup and waste disposal. Compared to traditional methods, electrostatic spraying offers a more efficient and cost-effective solution, contributing to overall operational savings.
References:
- Smart Pipe System for a Shipyard 4.0
- A Review on Industrial Augmented Reality Systems for the Industry 4.0 Shipyard